MAN BatteryPack
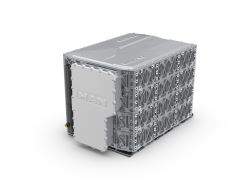
Through its MAN Engines business unit, MAN Truck & Bus offers industrial customers the opportunity to use batteries in their mobile and stationary applications. Applications in the agricultural machinery sector, material handling, railway applications, special vehicles such as airport equipment and municipal vehicles, but also marine applications are possible. In the field of electricity storage, there are numerous fields of application for charging concepts in the industrial sector, such as mobile power supply or fast-charging stations based on the principle of a power bank, as well as storage systems for renewable energies or peak load balancing. "We are already gaining initial experience with selected customers in classic applications. In the future, we will use this to develop future projects in mobile or stationary applications. These could be, for example, vehicles for autonomous freight or passenger transport or smart energy systems," says Jürgen Haberland, Head of Power MAN Engines.
MAN Truck & Bus already has many years of experience with batteries and battery packs through its many of the Group's own electrically powered commercial vehicles: the all-electric eTGE van was already marketed as a series vehicle in 2018, the medium-duty series of the battery-electric truck eTGM has been in customer use for urban delivery traffic since 2018, and more than 1,000 units of the Lion's City E electric bus have already been produced, bringing the total number of battery packs to over 6,000 in the Placed. With 260 electric buses in the first half of 2023, MAN ranks second in terms of new registrations in Europe. The next member of MAN's battery-powered, all-electric vehicle family will be the eTGX and eTGS heavy-duty trucks from 2024.
MAN BatteryPacks from Group-owned commercial vehicles
The electrically powered trucks and buses from MAN Truck & Bus are based on the MAN BatteryPacks, which MAN Engines is now adapting and marketing for other industrial applications. In general, a MAN BatteryPack – also known as a battery system – consists of several battery modules that are brought together in two to four layers in the battery housing. In turn, many battery cells are combined in each battery module. Due to the different arrangement options for the modules, differently designed MAN BatteryPacks can be produced. Each MAN BatteryPack contains 89 kWh of energy, of which 80 kWh can be used. Thanks to three different forms – from almost square to elongated – there are possibilities for integration into a wide variety of installation spaces. Currently, up to six MAN BatteryPacks can be combined with each other to achieve system capacities of up to 480 kWh net. A MAN eTruck of the heavy-duty model series thus achieves daily ranges of up to 800 kilometres.
In the context of e-mobility, the lithium-ion battery has gained the greatest importance in recent years. On this basis, MAN developed a special commercial vehicle-specific design of the battery cell with a focus on the properties of cell chemistry, charging cycles, mechanical robustness, vibration resistance and service life. The low weight and fast-charging capability make the nickel-manganese-cobalt (NMC) battery as a variant of the lithium-ion battery the means of choice for battery-electric commercial vehicle concepts.
Due to the great importance of cell properties for the performance of batteries, MAN plays a key role in determining the cell chemistry as well as the cathode and anode material. "We have numerous levers to create the best possible product for our customers, so we use them," says Dr.-Ing. Michael Bernath, Head of New Powertrain Components Development at MAN Truck & Bus. The requirements for the battery in the truck sector clearly exceed those in the passenger car sector: almost 500 kWh capacity, more than 8 years of efficient service life or mechanical load capacity of over 1.2 million kilometres, to name just a few. "The cell chemistry of our MAN BatteryPacks is designed to meet the highest demands. Our customers in the industrial sector also benefit from this," says Haberland.
Significant expansion of production capacities
In order to ensure that the strict requirements for the quality and safety of the batteries can be met, MAN Truck & Bus will manufacture the batteries in large series at the Nuremberg site from the beginning of 2025. The former international competence center for internal combustion engines is thus also developing into the linchpin for battery expertise in the MAN Group and is strategically realigning itself to this end. "In Nuremberg, we are bundling all key capacities, know-how and resources on the subject of batteries. This ranges from research, prototype development and construction, extensive testing, appropriate production design and manufacturing to dismantling, quality assurance and remanufacturing," says Dr. Markus Pröpster, Senior Manager at the E-Mobility Technical Center in Nuremberg. On an area of around 16,000 square meters, intelligently interlinked assembly and logistics systems can produce up to 100,000 battery packs per year. The groundbreaking ceremony on October 9, 2023, marked the start of large-scale battery production with an investment volume of 100 million euros.
The know-how for the development and production of high-voltage battery systems has been built up at the Nuremberg site since 2020 in the battery pilot plant as a pre-series center. To this end, massive investments have already been made in the infrastructure for the development areas in advance. Clear core competencies have emerged: These are the design and testing of battery housings, the assembly of battery systems, cell and module development as well as the development of battery management systems (BMS) such as control units, hardware and software for controlling the battery. "We offer the combination of the best cell and the best operating strategy and only then do we have the best possible properties for our batteries," says Bernath. The software is of fundamental importance here. The evaluation and virtual design of operating states and load cycles can have a significant influence on the service life and performance of the batteries. "We have been able to expand our knowledge of load profiles in the areas of on-road, off-road, power and marine over decades in engine construction. This means that we can now design the ideal battery not only in terms of hardware but also in terms of software," says Bernath. Through the strategic orientation of battery production and the use in Group-owned trucks and buses, MAN Truck & Bus, as a German commercial vehicle manufacturer, creates high standards in terms of quality, service life, robustness, temperature and extreme environmental conditions. Taking these factors into account, the topic of battery safety has been successfully researched through direct and indirect safety measurements in real test environments. Product improvements can also be continuously implemented with regard to the efficient service life on the basis of existing long-term experience. On the basis of these prerequisites, MAN Engines can work with customers from a wide range of industries, so-called OEMs (Original Equipment Manufacturers), to develop scenarios for original equipment (1st-life) or the secondary use of batteries that have already been used (2nd-life).
Experience in customer-specific development
As a business unit of MAN Truck & Bus, MAN Engines has been successfully developing customer- and application-specific solutions for decades with diesel and gas engines for applications in agricultural and rail technology, commercial and leisure shipping, and power generation. On the basis of the sophisticated combustion engines tested in commercial vehicles, engineers with the appropriate industry know-how further develop existing engines or assemblies and thus create leading drive solutions on the water and off the road. These experiences can be used identically for battery production for industrial customers. "Our battery customers benefit from the advantages of large-scale production and receive specific prototypes and small series optimally developed for their application at the same location. At the same time, MAN Engines operates a global service network, which will also be available to our battery customers in the future," says Haberland. Due to the prospective ramp-up of production to 100,000 MAN BatteryPacks per year in the next few years, external customers will be able to easily build on established processes and structures, for example to meet compliance with the European Battery Regulation, which pursues a complete lifecycle approach from procurement and production to use and recycling.
Closed recycling loop with different levels of use
When it comes to recycling, MAN Truck & Bus – and thus also MAN Engines – considers the entire life cycle of the battery up to recycling to be a closed loop. "The overarching goal in dealing with batteries is to close the material cycle in order to make a significant contribution to more sustainable development," says Pröpster. To this end, MAN will automatically assess the condition of batteries that are no longer suitable for use in commercial vehicles and then dismantle them. From the outset, different states such as shape, structure and manufacturer as well as properties of the battery are analyzed. For further use, reuse in the vehicle as a traction battery is considered after appropriate reprocessing. After the aforementioned factory repair (2nd-use) of the batteries or in the event that batteries are no longer suitable for stationary buffer storage of solar, wind or biogas plants after vehicle use or after an accident (2nd-life), recycling comes into play. MAN will implement a closed loop for battery raw materials with the primary goal of continuously extending the use of batteries and thus resources. Only when this is no longer possible will the valuable, recovered raw materials such as nickel, manganese, cobalt or lithium flow into the production of new batteries. For recycling, MAN prefers a mechanical process followed by hydrometallurgical processing. Through a mechanical and hydrometallurgical process, the valuable raw materials are recovered from the battery. MAN is part of the Volkswagen Group recycling network with recycling partners throughout Europe.